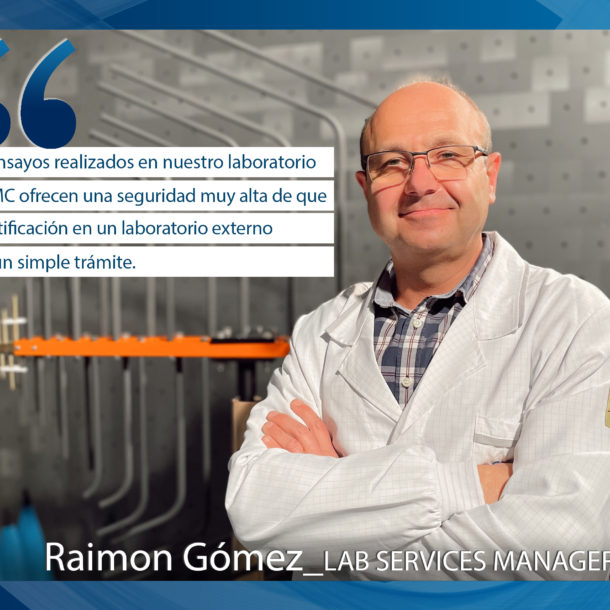
At DigiProces we manufacture products for a wide variety of customers, which means we daily deal with a lot of different references. This fact requires us to have a team with an agile answer ability in its DNA to be able to face sudden changes.
Every person becomes part of a gear assembly within the complex mechanism that our operations mean. This is the reason why everyone works under an individual development plan as a key point to reach maximum performance. We want each person to work focused on his/her strengths and concentrate in the job where he/she truly enjoys, making it easier to create and integrate high-performance teams.
Another pillar is our politics regarding update of machinery equipment and our maintenance program, which allow us to have the status of every asset under control to achieve maximum efficiency.
Excellence is a very ambitious word and it is always our goal.
We pursue it by increasing competencies and decision-making power of our employees while we continuously improve our internal procedures.
This concept is based on data acquisition and the capacity to analyze them in order to improve productivity. This is something strategically present in DigiProces vision from years ago, so the result is that we are on the way of becoming a Smart Factory.
At the production level, we are taking a giant leap in 2021, with new investments directly related to the digitalization of the whole engineering process and preparation of production, real-time data collection of machines performance and total product traceability during the production process and also regarding raw materials.
With Industry 4.0 implementations, we expect to reduce operations costs by 3,6% per year and also increase efficiency by 4,1% up to the end of 2021. We also expect to reduce cycle and lead times by 50%.
We have many automated operative processes currently going on, such as raw materials entry, components storage and supply to production lines, test systems, quality monitoring and expeditions. Progress is going towards automating the whole documentation process.
Gaining in intelligence of the production process, so that machines can communicate between them to correct flaws, will be the immediate consequence of implementation of this digitalization layer.
I would say is crucial. You cannot improve if you do not have data on what is happening. If you choose data properly and you are able to analyze them correctly, you can discover, for example, the root causes of potential production flaws, as well as detect where we have wastage and thereby eliminate it.
In the industrial revolution we are living, IT department plays the leading role. You can not consider evolve towards digitalization without an IT team with the same strategic vision, and I mean a team. The big leap is taken once it is understood that nowadays we can not move forward if we do not collect data and even more if we do not analyze them. A good planning of IT resources is very important to advance to Industry 4.0.
The budget for 2021 investment means a 6% of turnover and will be distributed both in software and hardware to implement MES (Manufacturing Execution System), a software focused on the control of production by monitoring and documenting management of the plant to improve OEE, and the change of our enterprise resource planning system (ERP/MRP).
Our future challenges are based on continue to grow sustainedly while adding value to our customers.
Solsonès, 87 – P. I. Pla de la Bruguera
08211 Castellar del Vallès. Barcelona