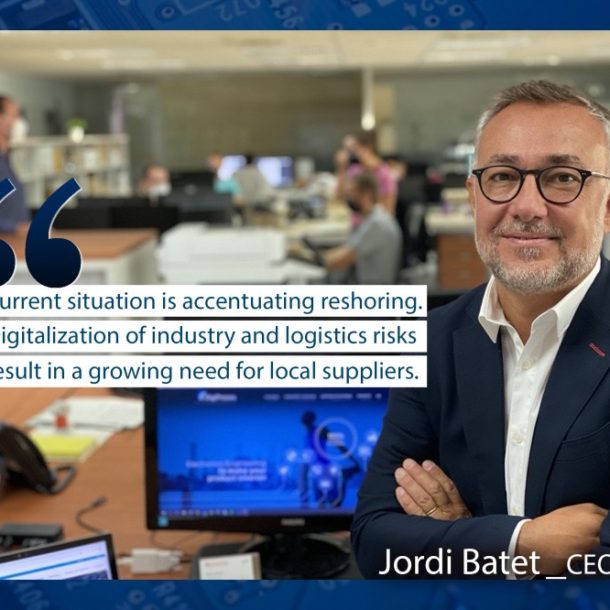
Production standards are determined by IPC-A-610 norm, which sets the acceptance criteria for electronics assemblies.
We also work under special regulations for customers in particular sectors such as automotive (IATF 16949) and medical (ISO 13485).
Product and process engineering teams carry out a feasibility analysis of any product likely to be manufactured at DigiProces in order to examine its peculiarities and ensure it can be manufactured under our production standards.
To be able to manufacture a product we need to control many factors: supply chain of components, definition of production optimal flowchart and availability of the staff and machinery required to perform manufacturing.
Flexibility is one of our greatest virtues. We adapt to the needs of our customers and offer all EMS’ services. We are quick in prototype manufacturing and competitive in large series production.
Being flexible allows us to work with different types of customers. Some of them only need SMT assembly and others want the product to be turnkey. In this case all stages of the project are included, starting with design, going through industrialization and ending with series manufacturing, which also covers test verification and final assembly of the product.
Relationship between factory engineering and the Tech Center is fluent and interactive. Designs must be functional, but also scalable. Precisely because of this, the Technology Center is in continuous contact with factory engineering to make sure the design meets the production standards and will be suitable to be manufactured repeatedly and efficiently.
On the way of transformation towards Industry 4.0, the mission of the Product Engineering team is the creation of the digital model for each one of the products we will manufacture to reduce the time-to-market to the maximum.
Yes, it is. DigiProces always seeks to position as best as possible against Asian competitors. Offering our customers competitive prices and delivery times are key factors we achieve thanks to many reasons. An important one is the project management provided by our process engineering, which is addressed to the production optimization. We design specific tools and conduct analysis on methods and times to reduce the cycle time.
Another important factor is our good management of the supply chain. We achieve so by establishing strategic agreements with the main electronic components suppliers so that we can have the best possible terms.
First thing we do is distinguish the typology of the product to be manufactured. We manage manufacturing differently depending on whether it is a New Product Introduction (NPI) or a production to be repeated, which we categorize as standard.
If we manufacture a standard product the production tracking is much easier and automated, following ITs reviewed and approved for each phase. On the other hand, if we manufacture a prototype or pre-series still classified as NPI, we apply special procedures for a continous monitoring of the product in the different manufacturing stages, giving support to the factory from each engineering department and obtaining the feedback required to document and prepare the next manufacturing of the product.
What added value services does Product Engineering offer?
From product engineering we offer our customers added value by seeking integrity of the documentary package we receive. How do we do it?
Our goal is the continuous improvement in all stages of the production process. To detect and implement these improvements we follow Kaizen philosophy and are also based on Lean Six Sigma procedures, which allow us to get rid of waste and, in short, increase efficiency and improve the quality of the final product.
The first strong point to highlight is our complete product documentation, starting with the feasibility analysis previous to quotation. In this moment we define criteria about actions and possible problems that may be found during manufacturing. This allows us to anticipate and manage with time enough all singularities coming with a new product.
Other key points are the planning to manage manufacturing of many references in parallel and monitoring of the product in the factory previously mentioned.
Finally, I would like to highlight traceability of the product. At DigiProces we guarantee traceability of all components assembled in the electronics, as well as the different processes the product has gone through. Therefore, we know exactly which PN was inserted in a particular position of the PCBA and we can keep track of the day and time when a specific part passed the functional test.
Solsonès, 87 – P. I. Pla de la Bruguera
08211 Castellar del Vallès. Barcelona