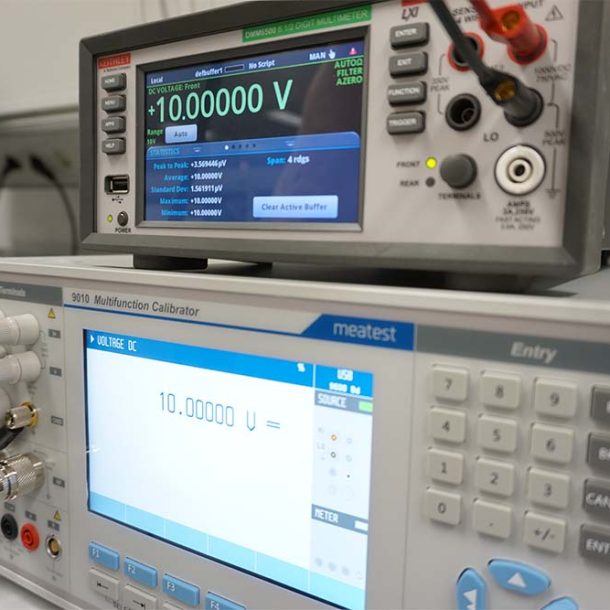
Interview with Engineering Manager at DigiProces, Josep Codina.
Improving business competitiveness is the main goal we work for and we are aware that digitalization and Industry 4.0 are two very important allies in our sector. We are currently implementing a MES (Manufacturing Execution System) system that is going to take us to a totally different scenario than the one we had until now.
Digital work instructions bring a wide variety of benefits. They allow us to always use the correct version and avoid doubts, and waste of time, as to whether the printed sheet is up to date or not. Also, because the instructions are built from the customer’s digital input data, there is less room for error than with conventional instructions.
They also allow us to have feedback from the operator in real time. In the event that he has doubts about how to assemble a component because the instruction does not explain it well enough, he/she can send a message to the process department to improve it. In this way, in a very short space of time the doubt is resolved and updated for this and all the operators who are using it.
On the other hand, saving paper is also a noteworthy aspect, since the effect that our actions have on the environment is important and we are committed to a sustainable business activity.
The process of defining a work instruction begins long before its own creation. When a customer places an order, the first thing is to digitize their product. We introduce the document package received to the MES system and then we define what production processes the product requires. Once determined, we assign the BoM components to be assembled in each one and with this information the MES automatically makes a work instruction proposal.
These types of automated work instructions work very well in processes where the main task is components insertion. Manual process instructions, such as assemblies, are created manually within the MES system with its own editor.
An important aspect to be configured when validating a work instruction is the complexity of the process to be developed. In our case, we have digitized the operational knowledge of each operator and in the work instruction we indicate the complexity of the process. In this way, an employee who does not have the necessary knowledge will not be able to open the instruction.
The step-by-step definition of each task to be performed makes the repetitiveness much higher. If we also add the fact that the operator must validate each of the steps completed in the work instruction, the consistency grows exponentially.
DigiProces went for automatic storage systems years ago to speed up the picking process and reduce the warehouse space needed.
Artificial vision is also very present in our day to day. We have been working with this technology in SMT processes for a long time and we are currently integrating it to verify the correct assembly of THT components as well.
We also have interconnected machines that, through point-to-point communication, use self-learning systems to improve their processes. With all the information that we are already collecting via the MES system, we will also develop this technology. In addition, with the test data of each manufactured product obtained through our Production Test Data Management System, we obtain very valuable statistics too.
The fact that all work instructions always have the same format, regardless of who created them, means that the operator is unconsciously familiar with the environment and the steps to be followed. With this standardization of work instructions we achieve a considerable errors reduction, as well as a significant training time shortening.
With all these strategic changes and new Industry 4.0 technologies that we are constantly implementing, our medium-term goal is to achieve production excellence. For us, this excellence means having more information to gain more flexibility, have a more refined production process and eliminate waiting times and also improve the quality of our processes and products delivered.
Solsonès, 87 – P. I. Pla de la Bruguera
08211 Castellar del Vallès. Barcelona